The Ultimate Guide to Manufacturing Plant Security
- Physical security
- Security for businesses
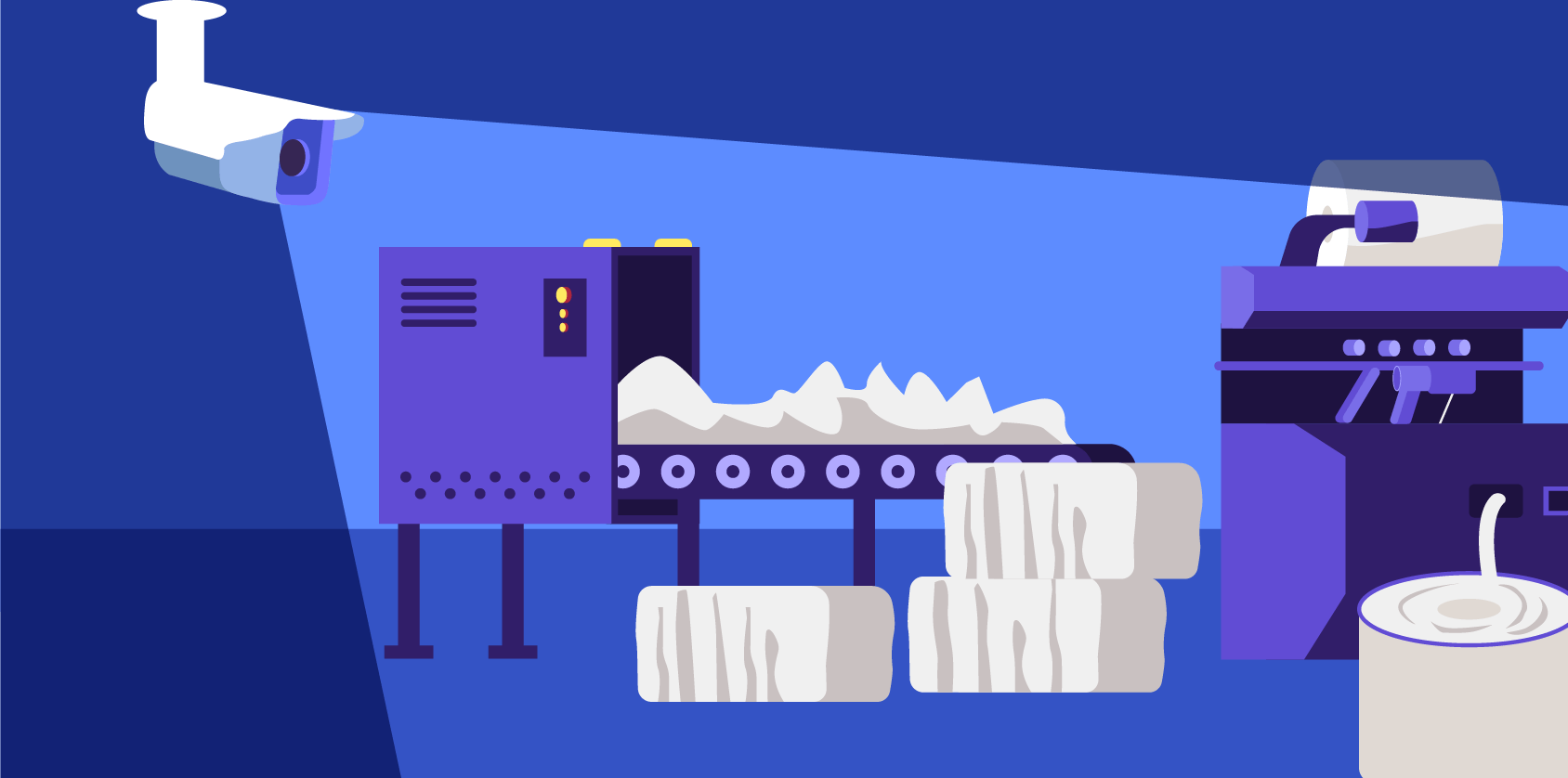
The manufacturing industry is key to multiple global supply chains, from critical infrastructure to food and drink. Manufacturers invest millions in resources such as machinery, tools, staff and products, not to mention raw materials.
These resources are necessary, but also expose manufacturing plants to risk. Any disruption to operations, no matter how small, can have financial consequences; both for the manufacturer’s bottom line and for supply chains.
Manufacturing decision-makers and security staff have a huge responsibility: to understand and mitigate all the possible risks that could have an impact on a manufacturer’s operations, assets, finances and reputation. In this guide, we go through practical steps every manufacturer should take to protect their plant from a variety of security risks.
Discover Calipsa's solutions for critical infrastructure security:
Conduct a risk assessment
The first and most important step to secure your industrial plant is a holistic, detailed risk assessment. An in-depth survey of your facility’s vulnerabilities will inform what types of security you need to invest in and how to implement your security strategy.
Manufacturing businesses face a variety of threats, from workplace accidents, to factory security breaches and supply chain disruption. Remember that risks don’t stop at your site’s perimeter; you should take into account global and regional risks as well as on-site factors.
There are also newer kinds of security and safety risks to consider when assessing your manufacturing facility. Nowadays, manufacturing technology is well integrated into many manufacturing processes, so it is just as important to identify cybersecurity risks as well as physical security risks.
Workplace safety is also paramount in the manufacturing sector, which has a higher rate of workplace accidents. Assessing health and safety risks is therefore essential for an industrial plant.
Establish security protocols for your manufacturing plant
Effective physical security in a facility or factory goes far beyond the basics of perimeter fences and access controls. To ensure your industrial facility is truly secure, you should use your risk assessment findings to establish comprehensive safety and security protocols for all members of staff.
Having security standards will help inform how you plan to secure your facility, but you must also check that they are truly working. For this, you should run regular penetration tests on your plant - these take place with the written approval of company executives, but without the knowledge of the rest of your employees.
These tests will survey how well the entire plant is secured, and how easy it is to gain unauthorised access. If unauthorised access is gained, testers will document it and report their findings in order to strengthen those weaknesses against future attempts.
How you handle the security risk of people entering and exiting your premises is another key consideration. Employees should be given tiered access control, depending on what they do and where they need to be. For example, if certain members of staff don’t need to access storage areas as part of their job, then they should not be allowed access. Similarly, you should set up protocols for visitors - they should be signed in and accompanied by a member of staff at all times.
Set up physical security measures
With all this in mind, let’s turn to methods of physical security that you should use to protect your plant. All industrial premises do well to have a secure perimeter, which includes a fence with gated and/or monitored entry points. This is important for vehicles that enter and exit your premises, particularly those that are bringing in raw materials and equipment, and which leave with your product.
Cargo trucks loading and unloading bays are real hotspots for cargo theft - making them one of the most vulnerable points on your premises. It is important to set up additional security here - whether that takes the form of physical guards, access controls, or extra security cameras. Employees have to sign off on deliveries and shipments, so it is crucial that they can account for goods and trace them if they do go missing.
Once you are on the premises, standard security measures such as access controlled doors, CCTV monitoring and alarms should all be in place. You should also ensure that you have the correct lighting conditions for your video surveillance to work effectively. If there are changing light conditions, for example with cameras rigged in outdoor areas, it is worth investigating whether you should install thermal cameras to support night monitoring.
To find out more about best practices for setting up video surveillance, check out our free whitepaper:
It is also possible to transform your security cameras from a purely reactive recording tool, into a proactive incident alert system with the help of intelligent video analytics. Analytics like Calipsa are easily integrated into many different camera types, and can quickly analyse footage to spot unusual activity that busy security professionals might miss.
Often, the security of a manufacturing plant falls to operations staff, who are called on to multitask. Analytics can help lighten the load on overburdened staff by sending alerts for activity that should be checked, such as people and vehicles. They can also filter out false alerts caused by activity such as trees or tarpaulins being blown around by wind. Discover our top 5 ways that your manufacturing plant security could be improved with video analytics here.
For particularly high-risk areas that members of staff can’t access, there is always the option of robotic guarding. These camera-rigged robots can patrol hazardous areas, and staff can monitor the footage to ensure that the area is safe.
Whichever security measures and systems you use, it is vital that you set up a redundancy network as backup. If your security systems experience an outage for whatever reason, having a secondary system to fall back on prevents your facility from being exposed to a whole host of risks.
Industrial health and safety
Your security measures should not only secure your plant but contribute to the health and safety of your workforce. When conducting your risk assessment, you should take into account the nature of your production processes - for example, do you work with fire, hazardous chemicals or combustible materials? If so, you should look into reinforcing your plant appropriately to protect against the risk of an accident: sensitive fire safety systems, regular fire drills and blast walls are some examples of how to mitigate these risks.
Similarly, if you use power tools or heavy equipment and machinery, it is essential that your staff have the appropriate protective equipment, safety training and protective measures in place to prevent accidents.
You might not realise it, but your video monitoring system is a valuable tool to help you establish and maintain health and safety standards in your facility. Security professionals and operations personnel can use cameras to monitor goings on around your plant, and if something looks out of the ordinary or unsafe (for example, a faulty production line) then action can be taken quickly.
Integrating intelligent video analytics can help make this process more efficient, picking up on anomalies or variations that busy staff might miss. Tools such as colour detection can trigger an alert if someone is not wearing a yellow vest, and motion detection can identify if machinery is not moving the way it should, or if there is an obstruction. Our resident manufacturing expert Kathee Mattern explains how cameras and analytics can help make industrial plants safer and more secure.
Manufacturing technology and cybersecurity
Most modern manufacturing processes are automated to some degree, as are most modern security systems. With so much of your infrastructure reliant on technology, it is crucial to pay the same level of attention to your cybersecurity risks as you do to physical security risks.
One area that you should pay particular attention to is your SCADA system. SCADA, or Supervisory Control Data Acquisition Systems, communicate with industrial control systems (ICS) to provide manufacturers with real-time information and analysis about their plant operations and processes. These systems combine hardware and software to allow manufacturers to gather data and manage processes remotely.
While commercial cybersecurity breaches cause inconvenient outages and some financial losses, a SCADA outage has much more serious consequences. SCADA is used to manage critical infrastructure, which means that a hack could cause massive disruption to industrial processes and supply chains, as well as posing a risk to the safety of your employees.
Similarly, if your plant depends on a smart security system, then an outage could leave your premises extremely vulnerable. Any other data storage systems you have, such as personnel, finances and your payroll, should also be protected with strong firewalls and malware protection. As with physical security, you should run regular penetration tests, establish cybersecurity protocols, and ensure you have a redundancy network in the event of a hack.
For more information about protecting your security network, read our complete guide to cybersecurity for video surveillance.
To find out more about what Calipsa can do to enhance the security and safety of your manufacturing plant, click here.
1 comment